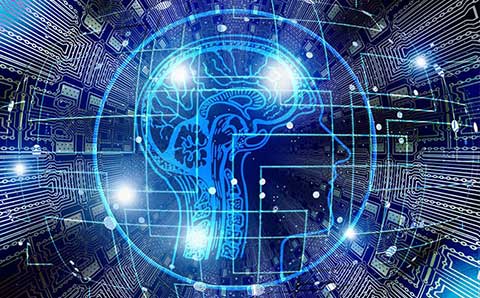
Key digital tech trends in petroleum industry
Key digital tech trends in petroleum industry
Oil and gas companies are investing in latest technologies keeping its benefits in sight.
The (not so recent) downturn in the oil and gas industry that started in 2014 has been a painful experience for many people. Everyone involved in the industry characterises it as the worst downturn to ever hit the sector and even those lucky enough to keep their jobs will have been affected to a certain extent: working in an environment of cost cutting and capital discipline with projects being postponed or cancelled all together.
he first real signs of a recovery came during 2016 and over the last few years, slowly but surely, confidence, growth and, perhaps most importantly, stability have all returned to the industry. Oil prices have stabilised (well, mostly) and costs have reduced markedly so that we now work in a much more efficient and streamlined industry. Companies are prepared for the ‘lower for longer’ environment and are continually looking to innovate and develop technologies to increase efficiency. The explosion in development of digital technologies during the past few years is beginning to change the way we work and these technologies are likely to shape the future of the industry over the next decade. But what are the key ‘digital technologies’ and how can they be applied within our industry?
Artificial Intelligence and Automation
Artificial intelligence (AI) is a term used to cover a wide variety of technological improvements and applications that involve machines ‘learning’ or ‘problem solving’, such as self-driving cars, understanding human speech (e.g. Apple’s Siri or Amazon’s Alexa) or competing in strategy games (e.g. chess). The potential applications for artificial intelligence and automation in the oil and gas industry are vast, from surveying and continuous monitoring, to planning and forecasting and improving safety. High risk environments such as an offshore rig or production facility can benefit from the use of both autonomous robotics and autonomous system monitoring to replace human presence in such high risk locations.
ExxonMobil, in partnership with MIT (Massachusetts Institute of Technology), are working to develop self-learning submersible robots for ocean exploration to boost their natural seep detection capabilities. In 2017, TOTAL announced the winner of a competition it funded to design an autonomous robot, the key functions of which were the ability to carry out inspections day or night, as currently performed by humans, together with the ability to detect abnormal equipment activity, such as a malfunction or leak, and intervene in the case of an emergency. Shell has developed a virtual assistant for its online customers where, via an online ‘chat’ interface, the virtual assistant can search hundreds of thousands of data sheets to recommend the right product based on their customers’ input.
The inspection of offshore assets is an interesting application for AI and automation. Details from a physical inspection can now be entered in real-time into a digital system using a hand-held device which can include information such as photos, measurements and location. This information can be automatically synchronised with an active database linked to maintenance scope and schedules accessed through a 3D representation of the platform, freely accessible to all. The system can then evaluate the results against pre-set limits and trending analysis such that key actions can be automatically generated and sent to the personnel required to perform the actions. This type of automation increases safety by reducing offshore time for personnel and by automatically flagging potential safety concerns and recommending action, whilst also reducing operational costs due to downtime and efficiency savings.
The majors are certainly leading the way in research and development of AI technology and automation, and with the potential safety advantages, not to mention cost savings due to increases in efficiency, we are sure to see a huge amount of investment and progress in this area in the next decade.
Big Data and Data Analytics
Big Data and Data Analytics: huge quantities of data can now be analysed to improve efficiency and safety in the oil and gas industry. Image by xresch from Pixabay.
The concept of ‘Big Data’, defined as increasing volume, variety and velocity of data, is familiar to the oil and gas industry. The industry generates a huge quantity of data, whether it is 3D seismic surveys, drilling data, production data or the monitoring of production facilities (pressures, flow rates, temperatures etc.). Our ability to generate, collect and store this data has continually increased, but this has brought with it problems with managing and analysing such vast quantities of information. Analysis of such data has been a major area of focus and innovation in the last five years within the oil and gas industry (as well as many other industries) with a view to potential improvements in exploration and production efficiency and safety.
At the present time there are many examples of research and development projects looking at how to utilise Big Data in the industry, but fewer real world examples of how Big Data are being utilised in practice. Research projects have covered applications in exploration, drilling, reservoir engineering and production engineering. Some examples include: the analysis of huge micro-seismic datasets using the Hadoop1 platform to model fracture propagation during hydraulic fracturing; the utilisation of Big Data to optimise steam assisted gravity drainage and cyclic steam operations on a heavy oil reservoirs by analysing data from over 14,200 wells in Chevron’s San Joaquin valley fields; and optimising the performance of electric submersible pumps (ESPs) by using data from over 200 million logs from 1,649 wells during a single year to evaluate ESP performance and identify emergency situations such as overheating and unsuccessful start-ups.
GE Digital, a GE Baker Hughes subsidiary, is an early adopter of Big Data analysis. GE Digital has developed ‘Predix’, a digital platform which can be used to produce ‘Digital Twins’ – software representations of a physical asset. The application’s machine learning algorithms are able to process a huge amount of data collected by sensors, such as equipment or parts performance, environmental data and weather conditions related to a processing facility. The algorithms then compare these against the ideal performance data contained in the database to search for discrepancies between the current and ideal state. If such discrepancies are identified, the application is triggered to send an alert to technicians, who in turn conduct preventative maintenance or part replacement.
Internet of Things and Electronic Monitoring
Internet of Things: the connection of sensors and monitoring devices over the internet has the potential to impact future production efficiency and oil and gas industry profits. Image by Gerd Altmann from Pixabay.
The internet of things or ‘IoT’ describes the extension of internet connectivity between physical devices and everyday objects. Embedded with electronics, internet connectivity and other forms of hardware such as sensors, these devices can communicate and interact over the internet where they can also be remotely controlled and monitored. Within the oil and gas industry, IoT devices and sensors can provide real time data on machinery, pipes, storage, transportation and employee safety, for example. With a total impact of many hundreds of billions of dollars estimated from oil and gas within the next decade, it is little surprise that the industry is showing huge interest in leveraging IoT.
The applications for IoT in the oil and gas industry, as with other digital technologies, centre on improvements in efficiency and safety. For example, by integrating the IoT into offshore equipment, employees can track and monitor equipment lifespan and other elements that can affect production, such as wave heights, temperature, and humidity. By applying this knowledge, companies can effectively maintain an offshore platform through predictive maintenance, helping detect equipment breakdown before it occurs. This leads not only to enhanced productivity with less downtime but also results in an improvement to the bottom line. In addition, this has the advantage of removing the need for physical presence and inspection in unsafe offshore environments. This type of application crosses over to other digital technologies such as automation, AI and Big Data analytics and is a good example of how new digital technologies can be integrated to achieve a positive result.
The ability to collect real time data via IoT, if funnelled into a suitable data analytics system, can have powerful advantages in improving efficiency, with only small efficiency improvements resulting in notable increases in production and therefore profits. Oil production captured in real time through embedded sensors linked to automated data communications systems can enable companies to collect information from assets anywhere and make informed operational decisions. For example, companies may be able to adapt real time drilling strategy and decisions based on comparisons of real time downhole drilling data and production data from nearby wells. According to Bain & Company, this type of data collection and integration has the potential to improve production by 6-8%.
3D Virtual Modelling and Drone Technology
Drone technology and outcrop modelling are already changing the way fieldwork is conducted and providing an invaluable new learning resource for geoscientists.
Some other emerging digital technologies that are having and will continue to have an effect on the way we work in the oil and gas industry are related to 3D virtual modelling and drone technology.
In the case of drone technology, this could have huge benefits in terms of monitoring and inspection of both inaccessible and/or dangerous oil and gas facilities. With the use of drones, visual inspections of such facilities can be carried out remotely, with high-quality images fed back in real time to drone operators. Multiple facilities can be inspected within a matter of hours rather than potentially days if inspections are carried out in person. This type of drone inspection can then identify genuine issues and problems and direct teams to deal with them immediately, improving efficiency by focussing on those facilities that require immediate attention. Another example is the inspection / maintenance of flares offshore. Difficult to reach and dangerous, this type of physical inspection can require production shutdown before it can take place, but with drone technology this inspection can be conducted at any time, saving costs and increasing safety.
In another application, drones can capture amazing images of rock outcrops, which, when combined with other technologies such as mobile mapping (helicopter) and laser scanning (LiDAR) data, can be georeferenced and processed to generate virtual outcrop models which can act as a very useful classroom learning aid. In addition, if data can be obtained from the outcrop via physical inspection these virtual models can be taken a step further where an accurate, high resolution 3D digital model of the outcrop can be generated which can be visualised and interrogated by the user. Some possibilities of data and visualisation from such models includes the extraction of 3D lines which can demonstrate clinoforms, channel bodies and sedimentary structure, fracture and fault geometry and facies boundaries. Additional information such as porosity, permeability and net to gross can be combined with information on the thickness and width of sedimentary features to create a powerful, interactive, learning resource that can be used to supplement more traditional classroom and field-based training courses.
Question and Challenge
It is clear that the oil and gas industry is starting to move towards a future of increasing digitisation. The benefits of increased efficiency, cost savings, improved performance and safety are becoming evident and companies who are investing heavily in developing these technologies will surely reap the benefits in years to come. Those companies who shy away from such technology will likely fall further and further behind the innovators over the next decade or so.
A word of caution though: as powerful as new technology is, in my opinion it is important that human input is not lost and that as oil and gas professionals we do not lose our core skills and that we truly understand the outputs of digital technologies. It would be all too easy to become reliant on new technology and in so many ways you could argue that we already are. However, technology does fail and the more reliant we are on it the bigger the impact of failure. We must continue to question and challenge the results of analysis and develop contingency plans in case of technology failure.
Source/Courtesy: GEO ExPro Magazine( https://www.geoexpro[dot]com)